K-Flex USA
In October 2016, K-Flex USA of Youngsville, N.C., contracted with Focus Design Builders of Wake Forest, N.C., MB Erectors of Millbrook, Ala., SNW Steel Services of Ringgold, Va., and Architect McGahey Design of Garner, N.C., to expand their facility. K-Flex USA is a leading manufacturer of flexible elastomeric, closed cell insulation products. They provide solutions for insulation applications across the plumbing, HVAC, Commercial/Industrial, Marine, Oil & Gas, Acoustic and OEM markets. The project would expand and add on to K-Flex USA’s already existing facility. The addition would include warehouse space and production space that would work alongside a connector building that would allow them to move product back and forth between the two facilities.
Problem
The company was looking to expand their USA operations to meet growing demand for their product. The expansion nearly doubled its operations. K-Flex also wanted to maximize space in the warehouse. Therefore, the team would need to accommodate clear heights, column spacings and column sizes to allow for maximum storage space. K-Flex also wanted to reduce costs of lighting. Another requirement was the need for a large dock area. The current dock area was a smaller space that caused a problem when trucks would line up down the street causing issues with entering and exiting the property.
Solution
Ceco Building Systems worked with Focus Design Builders on the K-Flex expansion project. The driving factors in choosing to build with metal were cost efficiencies and time savings compared to conventional construction materials. One piece of equipment for K-Flex’s production area was being manufactured in Italy and delivering in August 2017; choosing a metal building was the solution that met the demands of a tight schedule.
The building encompassed a rigid frame multi-span framing system that Focus Design Builders envisioned would give K-Flex USA the space it was looking for in its expansion. For the roofing system, McGahey Design and Focus Design Builders decided on 360,000+ square feet of Ceco’s DoubleLok® standing seam metal roof panel in Galvalume®. The roofing system also included a bar joist roof and 6” batt insulation. Due to the bar joist roof, utilizing DoubleLok® was the most cost-effective option. The product stored in the warehouse and the equipment used in the production area are sensitive to moisture, making the prolonged weathertightness of a standing-seam roof a must-have. DoubleLok® roof panels provided not only the cost effectiveness K-Flex needed but also the longevity for which they were looking.
For the building’s walls, 118,000 square feet of Ceco’s PBR wall panel in Signature® Light Stone were chosen. The interior wall system consisted of PBU wall panel liners in Signature® Polar White, partition panels and a wall translucent panel band. PBR panels were chosen due to cost effectiveness as well as the speed in which they could be erected. In warehouse buildings, it is not uncommon for panels to get damaged from equipment used to move the products. PBR panels were chosen because of their ease of replacement should any wall panels get damaged in the future by heavy equipment, trucks, etc. Ceco also provided a band of translucent wall panels for daylighting to help in the reduction costs of lighting. Lastly, McGahey Design and Focus Design Builders delivered on providing a larger dock area allowing for more trucks to be loaded.
Construction began in October 2016 and completed in July 2017.
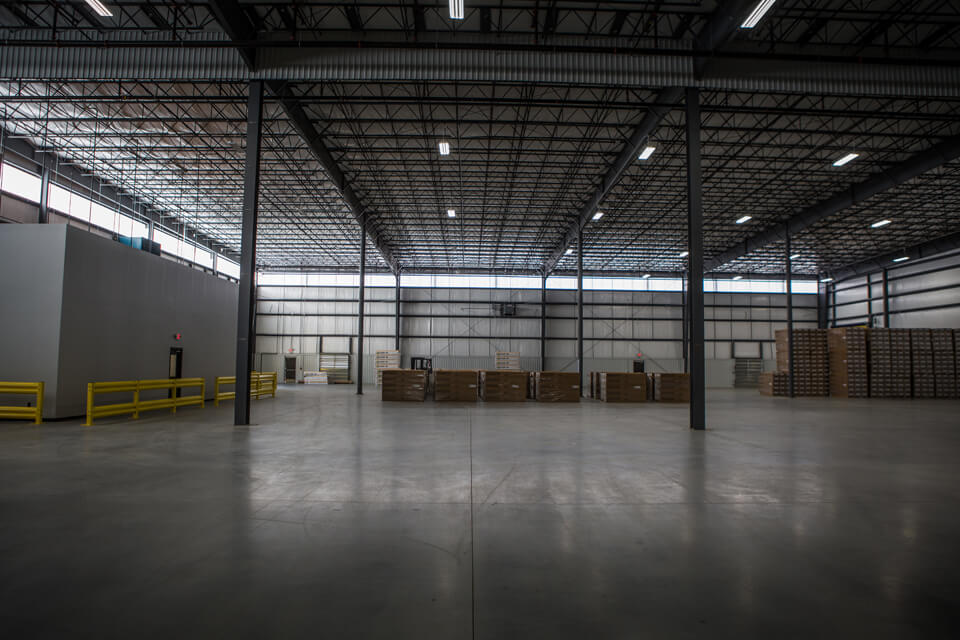
Project Specs
Ceco Products: Double-Lok®, PBR
Location: Youngsville, NC
Color: Galvalume® and Light Stone
Square Footage: 360,000 sq. ft.
Architect: McGahey Design, Garner, NC
Roofing Contractor: MB Erectors, Millbrook, AL and SNW Steel Services, Ringgold, VA
General Contractor: Focus Design Builders, LLC., Wake Forest, NC