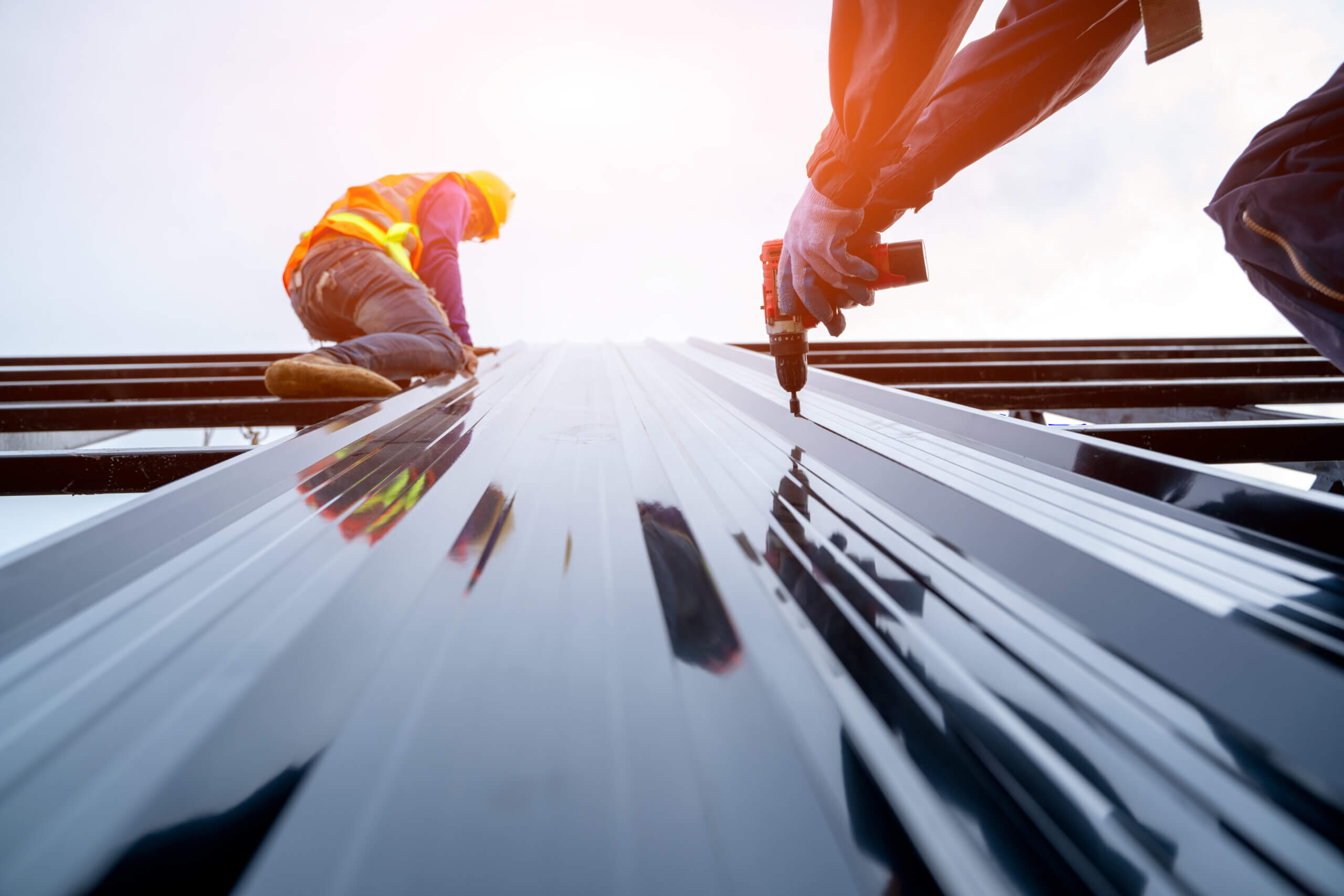
Posted on May 27, 2025 by Ceco Building Systems
May is Building Safety Month, a time to raise awareness about the importance of resilient and sustainable construction practices with safety standards in mind. At Ceco Building Systems, we’re proud to champion safety standards every day by designing custom-engineered metal building solutions that focus on the security and welfare of occupants while meeting local building codes for safety standards.
Why Building Safety Matters
Building Safety Month highlights the critical role that building codes and standards play in protecting communities. From safeguarding against natural disasters to promoting structural integrity, properly designed buildings are the foundation of thriving, secure environments.
At Ceco, we understand that safety isn’t just a checkbox. It’s a commitment. We work tirelessly to ensure every building we design supports safety standards and meets local building codes, providing peace of mind for our clients and those who use our buildings.
Ceco’s Commitment to Safety and Code Compliance
For over 75 years, Ceco Building Systems has been a trusted leader in the metal building industry, known for delivering durable, reliable, and resilient structures. Our buildings are designed to comply with the International Building Code (IBC), the American Society of Civil Engineers’ ASCE 7 standards, and other local and regional building codes. Here’s how we go above and beyond to ensure safety:
1. Custom-Engineered for Resilience
Every Ceco building is tailored to meet the specific environmental and structural demands of its location. Whether it’s designing for high-wind zones in hurricane-prone regions or accommodating heavy snow loads in northern climates, our engineering team uses advanced design practices to help ensure structural resilience. Our buildings are built to withstand extreme weather events, helping to keep occupants safe throughout seasonal conditions.
2. Fire Safety and Protection
Fire safety is a cornerstone of our design process. Ceco’s metal building systems incorporate fire-rated assemblies and materials that meet local building code requirements for fire resistance. By prioritizing non-combustible materials and integrating fire-protection features, we help mitigate risks for occupants and property.
3. Seismic and Structural Integrity
In regions prone to earthquakes, Ceco’s buildings are designed with seismic performance in mind. Our systems comply with seismic design categories outlined in the IBC and ASCE 7, helping ensure structural stability during seismic events. From robust connections to reinforced framing, every detail is engineered with safety standards in mind.
4. Sustainability Meets Safety
Ceco’s energy-efficient designs, including cool roof systems and insulated metal panels, help reduce environmental impacts and contribute to occupant comfort and safety. By creating eco-friendly and code-compliant structures, we support healthier, safer communities.
Partnering for a Safer Future
At Ceco, we believe that building safety is a collaborative effort. We work closely with architects, contractors, and building owners to ensure every project meets the unique safety needs of its community. Our nationwide network of Authorized Builders brings local expertise and a shared commitment to quality, helping to ensure that every Ceco building is managed with precision and care.
This National Building Safety Month, we invite you to join us in celebrating the importance of safe construction practices. Whether you’re planning a commercial, industrial, or institutional project, Ceco Building Systems is here to help you build with confidence.
Learn More About Ceco’s Safety Standards
Ready to start your next project with a partner you can trust? Explore our full range of metal building solutions and discover how we address safety, quality, and innovation. Contact our team today to discuss your project and see how we can help you build safe, strong, and smart.
Together, let’s make safety first, every month of the year.
May is Building Safety Month, a time to raise awareness about the importance of resilient and sustainable construction practices with safety standards in mind. At Ceco Building Systems, we’re proud…